2011 Newsletter
One Man’s Experience in Aquaculture
by G.C. Matthiessen
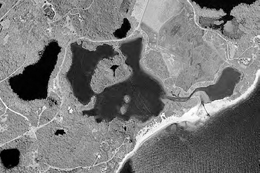
Aerial photo of Island Pond and surrounding ponds, April 2001. Island Pond, also known as “Oyster Pond,” has a peninsula jutting into it with a small pond at center. Courtesy of NYS Office for Technology
The following article appeared in Wrack Lines, Vol. 9 Issue 1 Spring/Summer 2009, and is reproduced with the kind permission of the author and the publisher, UConn’s Connecticut Sea Grant.
The annual harvest of seafood from the world’s oceans is currently between 80 and 90 million tons. During the past 60 years, world landings have increased by nearly a factor of six, and aquaculture now accounts for nearly 30% of total global fish production.
Although the practice of maintaining edible aquatic organisms under controlled or captive conditions is centuries old, aquaculture as an industry is relatively young and has grown extremely rapidly during the past 50 years. According to a Food and Agriculture Organization report in 2002, marine aquaculture production has increased at an average rate of about 10% per year since 1970. Aquaculture now accounts for about 27% of total global fish production.
In 1959, while employed by the Massachusetts Division of Marine Fisheries, I became interested in the potential for aquaculture on the island of Martha’s Vineyard. Of particular interest were the Island’s salt Ponds, several of which had over the years produced commercial quantities of shellfish, i.e. soft clams, hard clams, bay scallops and oysters. My interest lay chiefly in oysters, but, according to the records and anecdotal information, oyster production from these ponds had been inconsistent from year to year, for reasons not clearly understood.
During this time, I happened to visit my parents on Fishers Island, New York. My father kept a small aluminum skiff at the edge of a brackish water pond—Island Pond—and, in the process of hauling it from the water, I noticed a large number of juvenile oysters, or spat, attached to its bottom. A brief walk around the edge of the pond revealed a large population of oysters of varying sizes and year-classes, attached to the rocks.
I suggested to my father that Island Pond might be an ideal site to try culturing oysters on a commercial scale. He had retired from his architecture firm and was excited to become involved in a new project. He interested several friends on the Island and was able to put together a small corporation—Ocean Pond Corporation—of which he initially was president.
Island Pond differs from the salt ponds on the south shore of Martha’s Vineyard in several important respects. These Vineyard ponds are essentially shallow depressions in what was a glacial outwash plain. They are relatively shallow, with a maximum depth of 15 feet, and are much larger in surface area, two exceeding 1,000 acres in size. These ponds have a sand-silt bottom that affords little surface area to which oyster larvae might attach. Island Pond, on the other hand, is relatively deep, (maximum of about 23 feet), relatively small in surface area, (35 acres), and is surrounded for the most part by glacial till at the edge of the glacial moraine. It contains an abundance of rocks and the shells of dead and living oysters along its margins that provide an ideal surface for attraction of more oysters. The relative absence of such a substrate in the Vineyard ponds was perhaps a primary reason for poor oyster production. Ocean Pond Corporation was formed in 1962 initially for the purpose of producing marketable oysters for the half-shell market.
However, an examination of the oyster population in Island Pond indicated that there was little chance of producing quantities of mature oysters of half-shell quality from the pond. Because of the periodically low salinity of the pond water, the oysters usually had a bland taste, and their inner shells were apt to be riddled with mud blisters caused by the mudworm (Polydora websteri). Furthermore, the bottom sediment in deep water was too soft for oysters to thrive, and the firm ground in shallow water was not only limited in area but also infested with the predatory oyster drill (Urosalpinx cinerea). It was therefore decided to concentrate instead upon the production of seed oysters, which could be transplanted to other areas for growout and for which there was a strong demand in southern New England. For this purpose, the oysters would have to be cultured by off-bottom techniques that would minimize predation.
Initially, the raft culture system was employed. The rafts were constructed of Styrofoam logs surfaced with sheets of plywood. Beginning in late May, plankton samples were collected by towing a fine-mesh net through the water. When sampling indicated that oyster spawning had begun, usually between June and July, 16-foot strings of bay scallop shells were suspended from the rafts as cultch. During the first season of operation, a very satisfactory set of oysters was obtained, and within a few years, the number of rafts in use had risen to 150, capable of supporting nearly 100,000 shell strings.
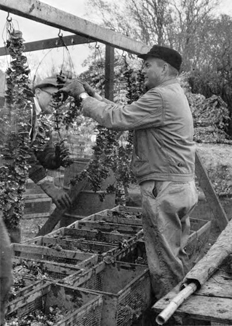
Harvesting Ocean Pond Corporation oysters, 1966 – Museum Collection
The strings were left suspended in the pond until the following spring. Shells bearing the juvenile oysters were then stripped off the wire strings and loaded aboard oyster boats at the Fishers Island dock, later to be spread on private beds in New York, Connecticut and Massachusetts. A single years’ harvest might exceed 100 million oyster seed.
During these early years, most of the seed was sold to large oyster companies in Long Island, New York, which were experiencing a series of poor oyster sets. Later on, I joined Dick Nelson in ownership of the Cotuit Oyster Company on Cape Cod, and many of the seed oysters produced in Island Pond were planted in Cotuit Bay. Natural sets in Cotuit Bay were rare, but the quality of the mature oysters that grew there was exceptional. After the beds had been scraped clean of algae and predators, the seed oysters were spread over the bottom, where they remained until reaching marketable size.
This operation continued for 12 years (1962-1973) but was temporarily discontinued after 1973 due to a number of factors, the primary one being uncertainty of oyster reproduction, i.e. erratic setting in the pond from year to year.
Another factor was the inability to control setting intensity. Severe overcrowding of oyster spat on the shells, as frequently occurred, was discouraging to the buyers, since this could result in slow growth and high mortalities, and the survivors were often stunted and misshapen. Finally, by the 1970s, hatchery production of oysters had grown more reliable, offering certain advantages such as choice of parent stock and control over setting intensity.
In 1977, the Corporation obtained a small sample of “cultchless” seed from Maine. These tiny oysters, spawned in a hatchery, had set on small particles of shell that had been ground down to a fine size. These seed, growing singly, for the most part, eventually resulted in well-shaped adults free of clusters and well suited for the half-shell market. The single oysters were much preferred over the wild oysters obtained from Oyster Pond and revived interest in oyster culture in New England.
The seed were placed in floating fly-screen trays moored in Island Pond in early summer. Every few days, the trays were flipped over and exposed to the air and sun in order to avoid fouling of the mesh. By the fall, the oysters had experienced little mortality, were over an inch in size, and were considered large enough to plant on the oyster beds of commercial growers.
These results were sufficiently favorable to encourage expansion of the floating tray system, which eventually involved more than 500 trays. In the fall, when growth had ceased, the trays were removed from the water and brought ashore.
When the availability and/or quality of seed oysters from commercial hatcheries became inconsistent, the Corporation developed its own hatchery system as an emergency backup in 1979. The original hatchery consisted of a small wooden frame structure built at the edge of the pond and covered with clear fiberglass panels. It was large enough to accommodate ten large plastic containers which served as larval tanks. Pond water was supplied to the hatchery through a garden hose connected to a small electrical pump. The entire structure was disassembled each fall to avoid wind damage during winter.
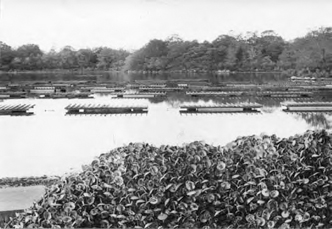
Ocean Pond Corp. rafts on Island Pond, 10/15/72 (Note strings of scallop shells in foreground) – Museum Collection
When the pond temperature in late spring rises to about 21oC, the majority of the oysters in the pond are ready to spawn. In 1980, ripe oysters were collected from submerged rocks and placed on black plastic in shallow dishes which were exposed to the sun, causing the temperature in the dishes to rise to about 30oC. The oysters were then stimulated to spawn by macerating one of the ripe oysters in a Waring blender and adding a sperm or egg suspension to the dishes. The eggs obtained from the spawners were mixed in a bucket with a small quantity of sperm and transferred to the larval containers.
Algal food for the larvae was obtained by fertilizing a series of 100 gallon outdoor tanks with nutrient-rich water pumped from the bottom of the pond. Phytoplankton blooms, consisting primarily of microflagellates and small diatoms, would usually occur in the tanks within a few days and supply the food for the larvae. Most of the larvae would attain setting size 10 days or so after fertilization.
When the larvae were ready to set, they were transferred to shallow trays with fine mesh bottoms in which tiny particles of dolomite or ground oyster or bay scallop shells had been spread as cultch. These buoyant trays were then placed in the pond in shallow water. After two to three days, the shell particles with spat attached were transferred to the standard flyscreen trays described earlier.
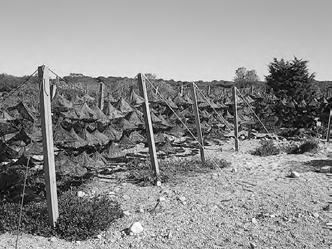
Pearl nets being air-dried to reduce fouling, 2003 – Courtesy of F.I. Oyster Farm, Inc.
This was a primitive culture system, justified only by its simplicity and minimal expense. Production depended to a large extent upon weather conditions. Extended periods of cold and cloudy weather limited the algal food supply by delaying the development of the pond’s nutrient-rich bottom layer, which depended upon thermal stratification. Poor weather also discouraged algal blooms in the outdoor tanks and slowed the development of the larvae. Nonetheless, barring unfavorable weather, this system proved to be a valuable supplement to the numbers of seed oysters obtained from other hatcheries. In some seasons, it was the only source of supply.
During the 1980’s, the culture system at Island Pond underwent a series of changes. The use of floating wooden trays for growout was eventually abandoned in favor of pearl nets, which required little maintenance and avoided the need to transfer the slow-growing oysters to submerged trays in the fall because of storms and ice. By shifting to pearl nets, that procedure was eliminated, since the nets, suspended from buoyed long lines, could be positioned beneath the surface. The only drawback, and the one affecting all suspension culture systems, is that the nets can be subjected to intensive fouling. Fouling was controlled by air-drying the nets on warm sunny days or by power washing.
Procedures for algal food culture for the larvae also underwent a series of changes. The floor space inside the hatchery facility was enlarged and the walls insulated. Algal cultures—small diatoms and flagellates—were obtained from regional laboratories and used to inoculate larger containers—plastic carboys and fiberglass tubes. These were held under florescent lights and aerated inside the hatchery. The algae cultures provided the food for the larvae that were held in 100 gallon conical fiberglass tanks. As the larvae developed to setting size, they were transferred from the conicals and placed in shallow trays with fine-mesh screening. These trays were held in rectangular tanks filled with preheated seawater. Finely ground oyster shell was spread thinly over the bottom of the setting trays. The newly set larvae were held in this system for 7-10 days, by which time they were usually large enough to be moved outdoors.
When setting was completed and many of the oysters had reached 0.5mm in size, they were transferred to silos held in outdoor tanks into which pond water was pumped continuously.
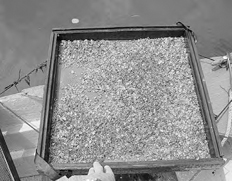
A tray of juvenile oysters, 2000 – Courtesy of F.I. Oyster Farm, Inc.
Twice each week, the oysters were sieved through a series of screens. Those retained in the 1.0 mm sieve were transferred to floating fine mesh screens in the pond. Within 2 weeks of spawning, setting usually was completed, and, after 3-4 weeks, all the juveniles were transferred to an outdoor upwelling system.
An alternative system also used involved upwellers. This consisted of placing the juvenile oysters into a series of silos held in outdoor tanks into which pond water was pumped continuously.
In this type of system, the water flowed upward through the bottom of the silos and then returned to the pond. The juvenile oysters subsisted upon whatever planktonic food was available in the pond water.
During the mid-1980’s, the advantages of producing and selling oysters that had been grown in the pond for two growing seasons rather than just one were explored. The primary objective was to determine the technical and economic feasibility of suspension culture on a commercial scale. Off-bottom culture of shellfish assures a higher rate of survival than the on-bottom methods, which often incur heavy losses from predation and/or siltation.
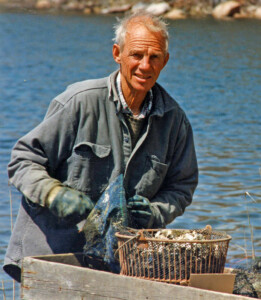
Carey Matthiessen
For purposes of culturing the oysters in the pond for a second season, 5-tier lantern nets with 12 mm mesh were utilized for the growth experiments, using one-year old oysters. By the end of the growing season, these oysters had roughly doubled in size with respect to growth of shell. However, none had reached a minimum acceptable marketable size of three inches. Furthermore, the tendency of many of the oysters to grow into the meshes of the net, combined with fouling of the nets by algae, tunicates, and other marine organisms, including wild oysters, required continual maintenance and added significantly to the overall cost of the operation. Moreover, many of the oysters were heavily infested with Polydora, which reduced their marketability.
In 1985, Ocean Pond Corporation abandoned the use of wild pond oysters as brood stock and concentrated upon breeding a strain of oysters obtained from Rutgers University. This particular strain of oysters proved to be distinctly superior to the native pond oysters in terms not only of disease resistance but also of growth rate. A significant percentage of each year’s production has reached market size at only 18 months of age.
Production in Island Pond is vulnerable to two natural phenomenon; hurricanes and disease. Since changing the culture gear from surface trays to nets suspended from long lines, the chances of more damage from violent storms is much reduced.
The possibility of disease is more insidious. Island Pond is characterized by high summer water temperatures and a salinity range favorable to both Haplosporidium nelsoni and Perkinsus marinus. Fortunately, the occurrence of these pathogens has been rare.
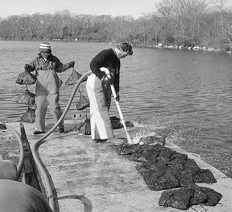
Oyster Farm employees power washing shellfish to control fouling, circa 2003 – Courtesy of F.I. Oyster Farm, Inc.
During the 30 years or so that I worked at Island Pond, I met, and hired, a good many people interested in working—full or part time—for Ocean Pond Corporation. Several of the employees left the company after a few years to start their own oyster companies, all of which have been successful: Joth Davis on Bainbridge Island, Washington; Bob Rheault at Point Judith, Rhode Island; Seth Garfield on Cuttyhunk Island, Massachusetts; and Steve Malinowski on Fishers Island, New York. Steve Malinowski, who assisted Ocean Pond Corporation in many ways, acquired the company after I retired, and the company now goes under the name of Fishers Island Oyster Farm.
About the author: G.C. Matthiessen is a marine biologist and previous owner of the Ocean Pond Corporation, Fishers Island, New York. He served as President of Marine Research, Inc., a consulting firm in Falmouth, Mass., and as Chairman of the Board of Directors of The Sounds Conservancy. He also served for many decades as a Trustee of the H.L. Ferguson Museum, Fishers Island, New York. Now retired, he lives in Sanibel, Florida.